Coosa Steel Corp is a family-owned, full-line steel service center that provides a wide range of steel products, including hot rolled and cold finished steel, stainless steel, galvanized steel, aluminum, and alloys. One of their core products is custom designed, portable steel stacking racks for flexible material handling in warehouses and manufacturing areas. 95% of these rack units are custom built to customer specifications.
In 2018, Andrew Saville, Executive VP and General Manager at Coosa Steel Corp, reached out to Kentucky Gauge to help improve their drilling operations. At that time, they were still manually drilling their custom racks using multiple drill presses and were needing a faster, more efficient way of drilling repetitive holes.
Enter the Kentucky Gauge KDP line of custom drilling systems.
The Problem
Coosa Steel Corp wanted to get into different rack types that require several holes in tubing, channel, and angle. The channel and angle were simple with a hole punch, but the tubes require drilling. It started as small jobs, 100-200 racks, but it quickly blossomed into thousands of these.
Coosa Steel Corp was continuously drilling 9/16″ though holes in 2″ x 14-gauge x 96” long steel tubing. Each tube required two different drill setups:
- One drill to drill pilot holes.
- One drill to the drill the pilot holes to size.
With this two-step, manual process, holes were often not centered or not drilled all the way through, which caused constant problems when assembling the racks in the field. Coosa Steel Corp needed to find a better, more consistent way to drill these tubes.
They initially explored getting a tube laser, but the startup costs involved with a tube laser were too high, which led to searching for a more economical, yet robust and reliable drilling solution. Andrew knew he wanted opposing drill heads and since the parts were repetitive, manual adjustments in the Y-axis and Z-axis were acceptable as long as the X-axis was automated to eliminate operator interactions.
The Solution
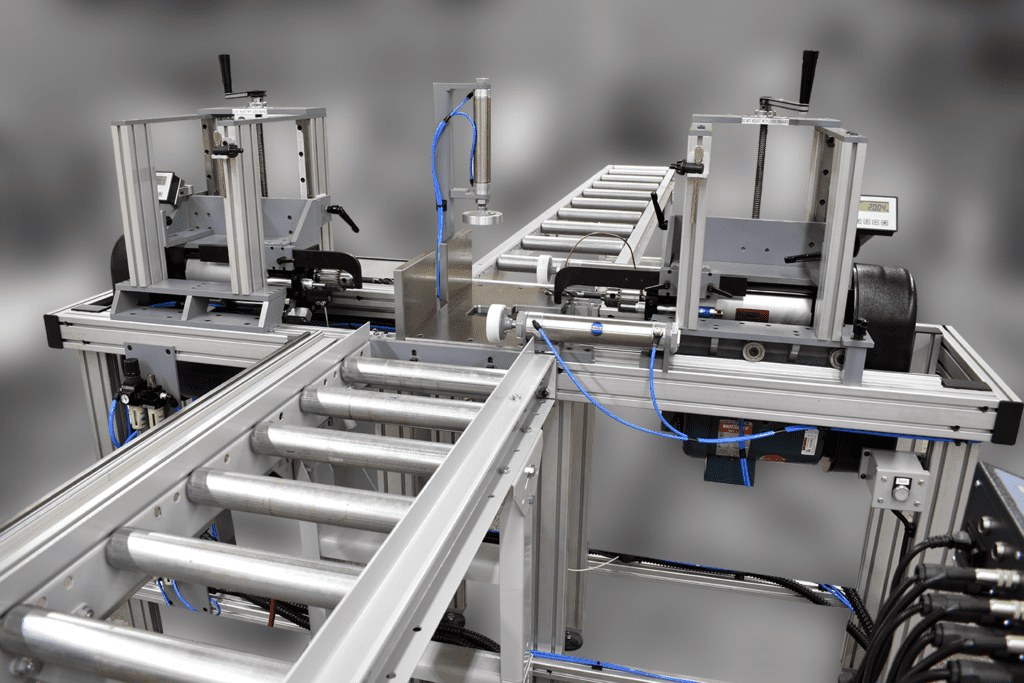
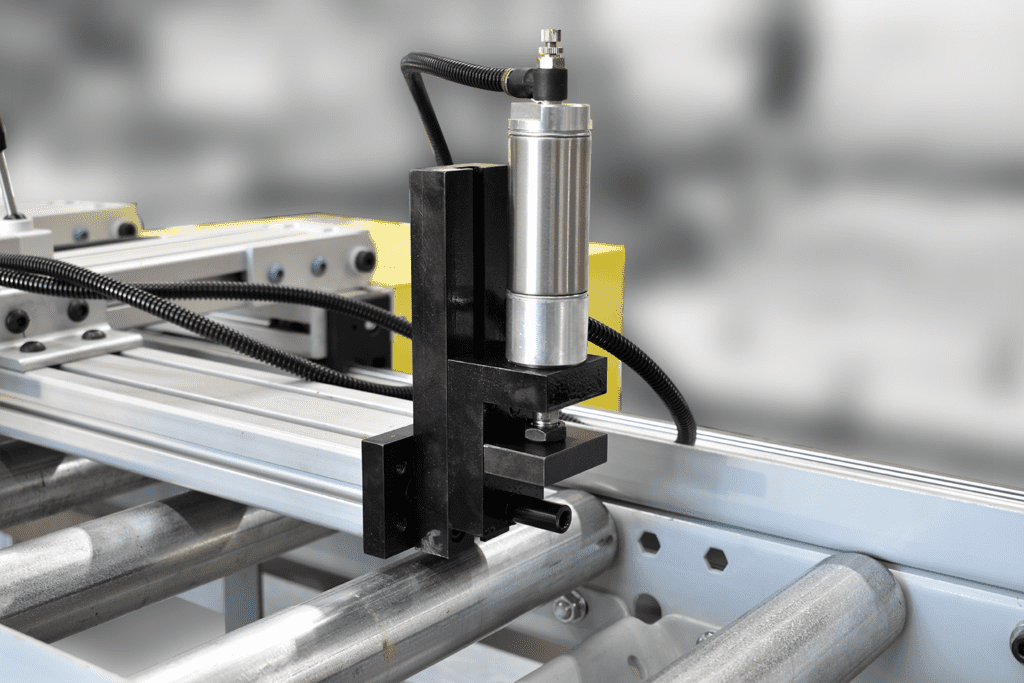
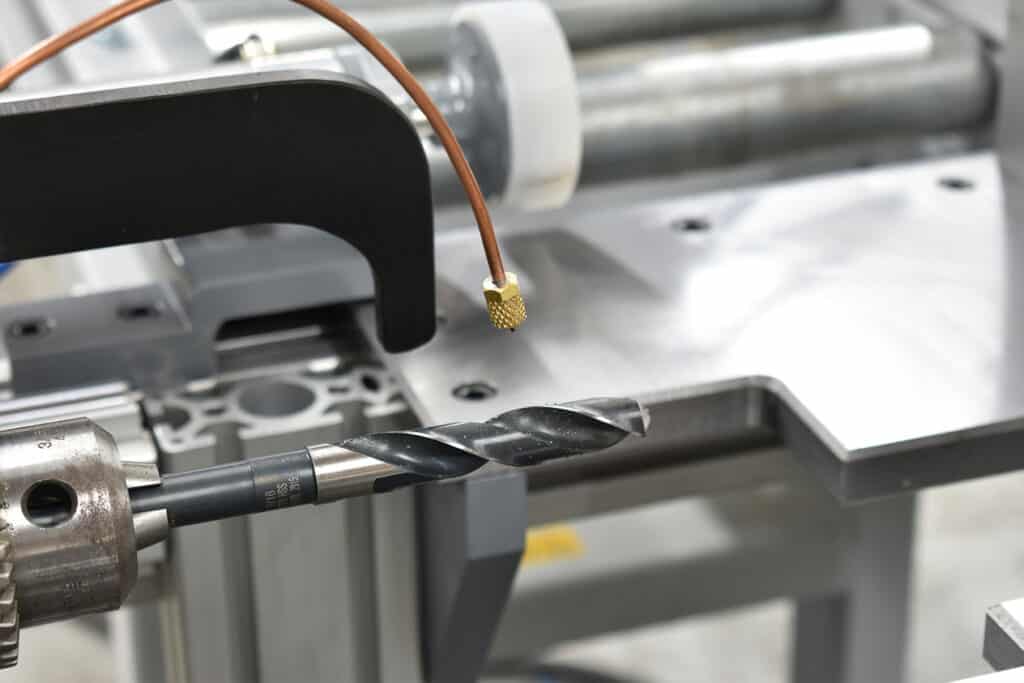
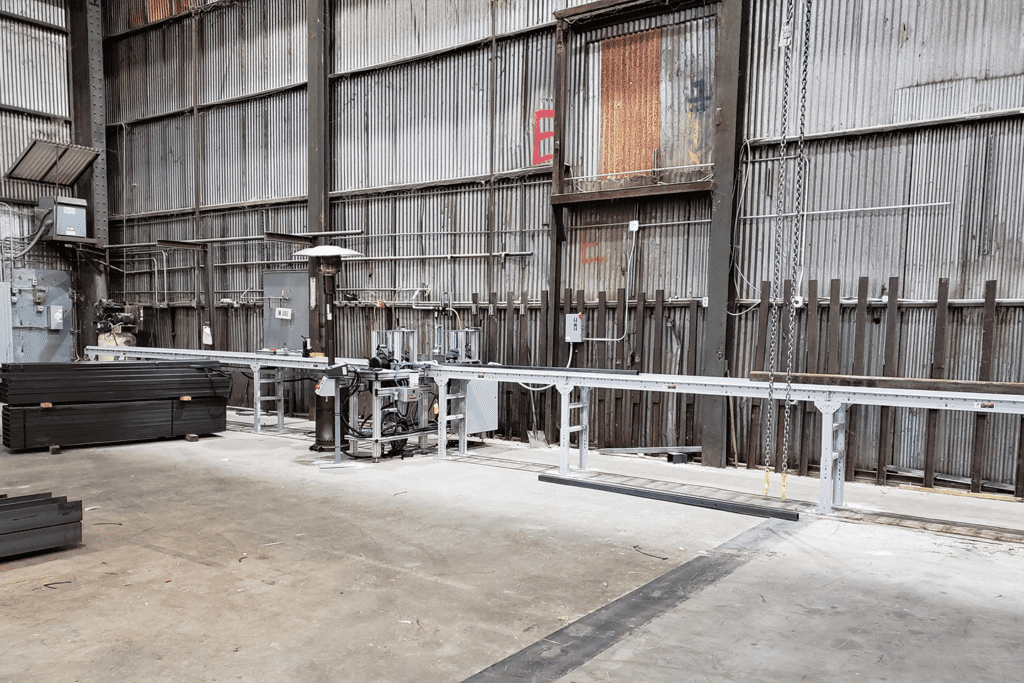
Key Features and Specs:
- Turnkey automated drill line.
- Two horizontally opposed pneumatic drilling units capable of drilling up to 3/4″ holes in steel tubing with wall thicknesses up to 1/2″.
- Drill height adjustments via hand crank and digital readouts for positioning to various centerlines.
- Oil misting system for drill bit lubrication.
- Adjustable proximity sensor for drill stroke depth control and proof of drill return.
- Heavy duty 20ft servo-driven tube feeder capable of feeding up to 1/2″ x 6.5″ square steel tubing with weights ranging up to 850 lbs.
- Custom tube gripper to hold tubes during feeding process.
- Repeatability: ±0.001″
- Adjustable proximity sensor for drill stroke depth control and proof of drill return.
- Fully automated tube processing to user-programmed hole patterns.
- Up to 32000 program steps available at the keypad with program download feature from a connected or networked PC.
Benefits and ROI
After the drill system was installed at Coosa Steel Corp’s facility in Rome, GA, production immediately skyrocketed from 40-50 tubes per day to drilling 300-400 tubes per day. That’s a production increase of up to 900%! Because of such a drastic increase in production and greatly reduced lead times, Coosa Steel Corp’s racks division grew to approximately 50% of their total sales, which more than doubled their business.
The repeatability and accuracy of the hole placement, along with the huge reduction in labor, were among the most coveted benefits. But the most satisfying aspect of the drilling system was the ROI.
Amazingly, based off what we were able to do, it paid itself off in 2 weeks just based off the increase in sales and the decrease in labor. Seriously, 2 weeks.
Andrew SAville, Executive VP and General Manager at Coose Steel Corp
According to Andrew, Coosa Steel Corp initially had no way to reasonably drill their tubes, but after the new drill system was installed, they were able to grow their racks division to a point where they can efficiently add holes to every rack they offer now. With the money made and saved since installing the Kentucky Gauge KDP, they were finally able to purchase a BLM tube laser. However, four years later and even with the laser, the drill system is still relied on for drilling material larger than 6″ x 6″ or heavier than 13 lbs./ft. “I would love to know exactly how many holes that machine drilled. I bought it as a 3-4 day, 1 shift per day machine. Before the tube laser arrived, we were running it 2 shifts 6 days a week.”