As a leading supplier of customer-oriented solutions, AKG has acquired an internationally acclaimed reputation for producing reliable, high-quality heat exchangers specializing in brazed aluminum bar-plate construction as well as traditional copper/brass tube & fin designs. AKG products can be found in the construction, forestry, agriculture, on-highway, compressor, material handling, industrial, off-highway, and mining markets.
In 2019, AKG of America contacted Kentucky Gauge to help improve the manufacturing process for their surge tanks. The cost of outsourcing the surge tanks was quite high and they were looking for a way to bring the process in house to reduce manufacturing costs. AKG chose to order a PMI-20 upcut saw from Pat Mooney Saws and sent it to Kentucky Gauge for integration with a 26ft PD100 pusher system. This provided a fully automated cutting cell for the parts that form their surge tanks.
We recently had the pleasure of catching up with Raghu, a Manufacturing Engineer at AKG and he was kind enough to provide us with his feedback. Raghu was instrumental in spec’ing in the original PMI-20 and PD100 system and was so impressed with its performance, he spec’d in and ordered a second one for a separate facility!
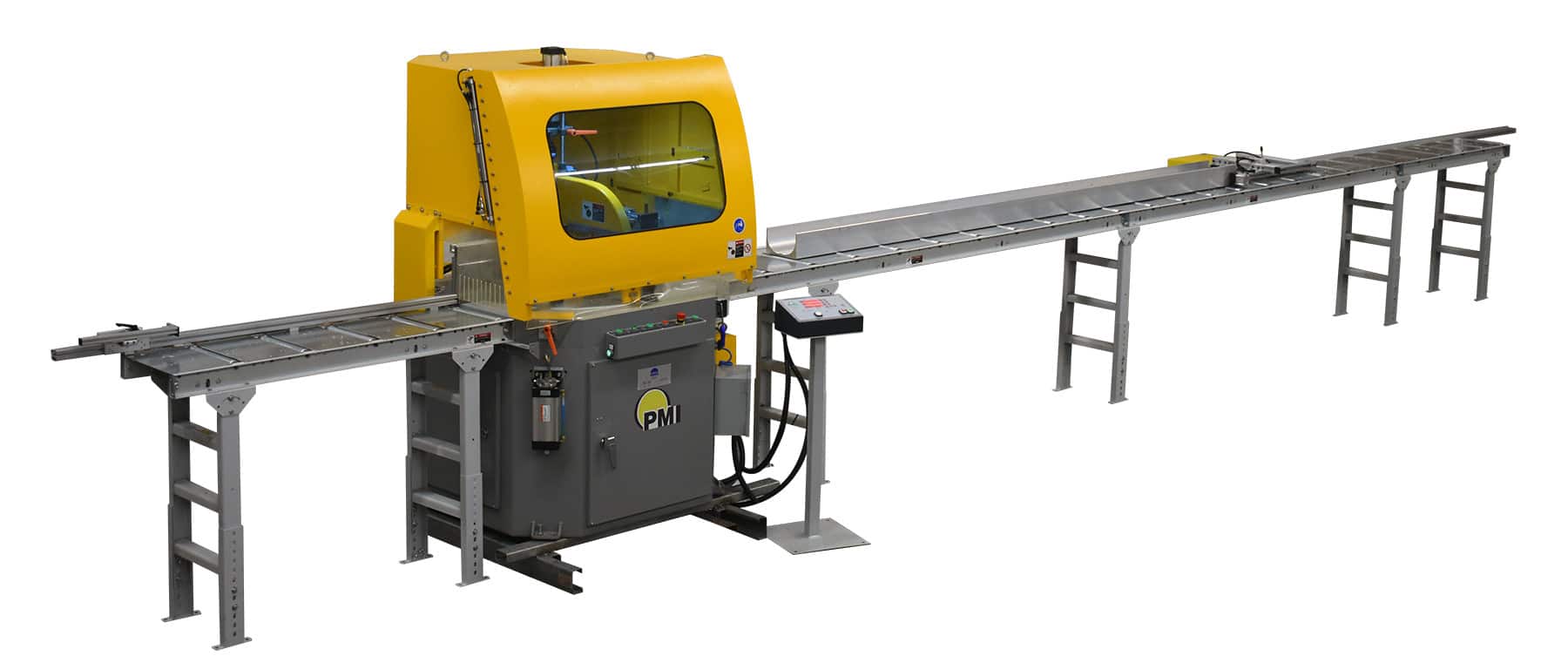
Why did you choose Kentucky Gauge over their competitors?
We actually were introduced to Kentucky Gauge by their competitors! When we compared the specifications of the machines, our choice was very simple. Kentucky Gauge was superior in value and product. I couldn’t have asked for more. One of the more notable points was Kentucky Gauge uses a linear encoder and their competitors use rotary encoders. The position accuracy for the linear encoder is ±0.001″, whereas the competitor’s rotary encoder was ±0.004.
How were you measuring and cutting parts prior to adding this new system?
We used to measure with a tape measure. Now, with the Kentucky Gauge, we save the time that was wasted with manual measurements. We have a lot of confidence in the dimensional accuracy of the part from the time we implemented Kentucky Gauge.
What benefits, advantages, or improvements have you seen with the PMI-20 and Kentucky Gauge PD100?
- We are able to cut all of our integrated surge tanks now and reduce the labor costs to produce surge tanks. It also allowed us to produce integrated surge tanks for our sister companies overseas.
- By opting for a fully automatic sawing system with the Kentucky Gauge, we are able to save at least 2 hours/day of actual production time. We were able to reduce the setup time to under one minute, which was previously 15 minutes with our old process.
- The automatic positioning has eliminated operator errors, and the increased part accuracy has greatly helped reduce downstream labor. Previously, with manual positioning, we were required to add shims to the parts to compensate for errors, and with automatic positioning all that is gone.
- Operator fatigue has been greatly reduced because the PD100 advances the parts instead of the operator manually pushing it.
- Due to the cut accuracy, we can achieve with this system, it serves as a critical back up if our other profile saws go down.
- The cost of the system is at least 40% below other similar saw and pusher setups.
Would you recommend Kentucky Gauge?
Definitely! I think their service manager is the best (shout out to Joe Murphy). I deal with several companies and different kinds of machines, but in my experience, I can attest that Kentucky Gauge sales and service support is exceptional – they really care. There are several instances where they went the extra mile to make sure that our production issues are resolved.